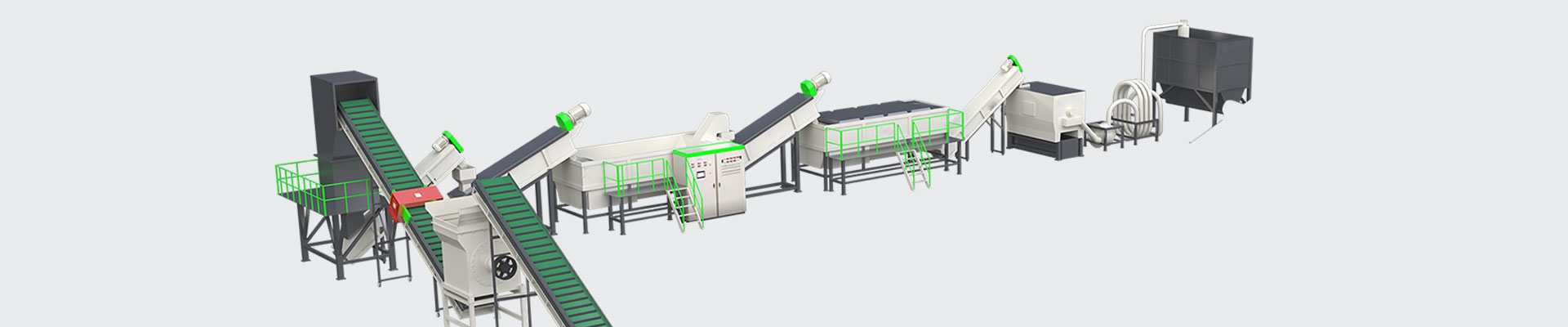
PP woven bag pelletizing line
Recycle the plastic waste to make profit
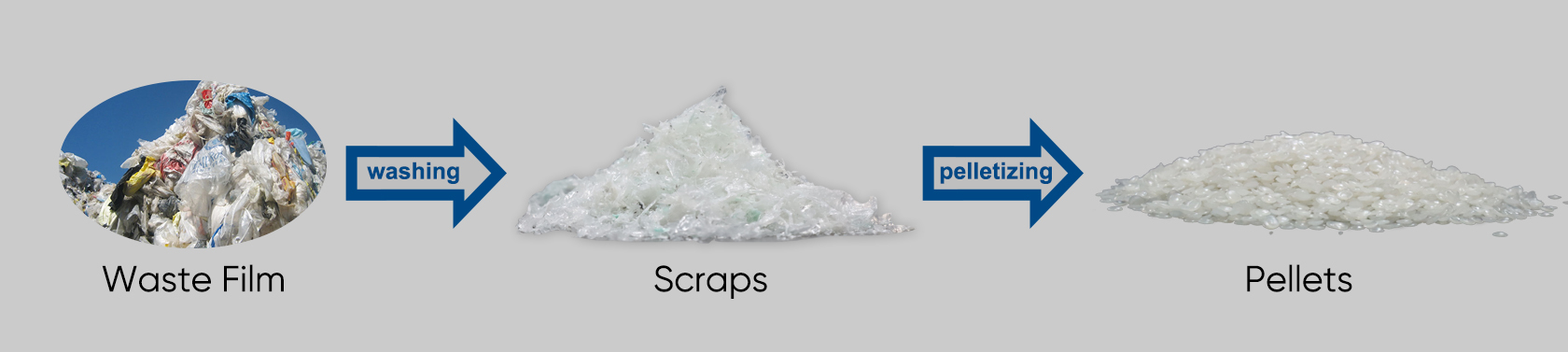
APPLICABLE MATERIALS
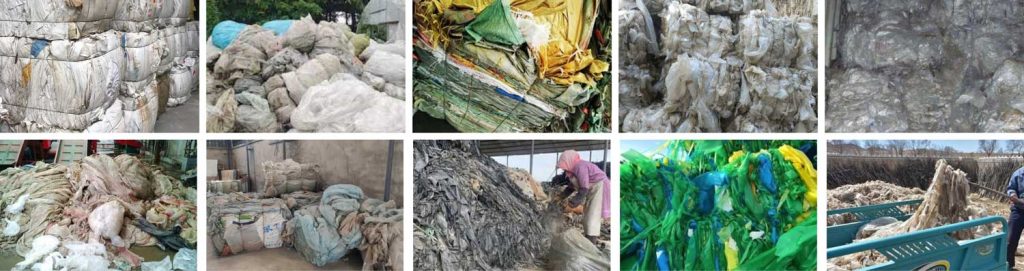
BRIEF DESCRIPTION
WORKING PROCESS
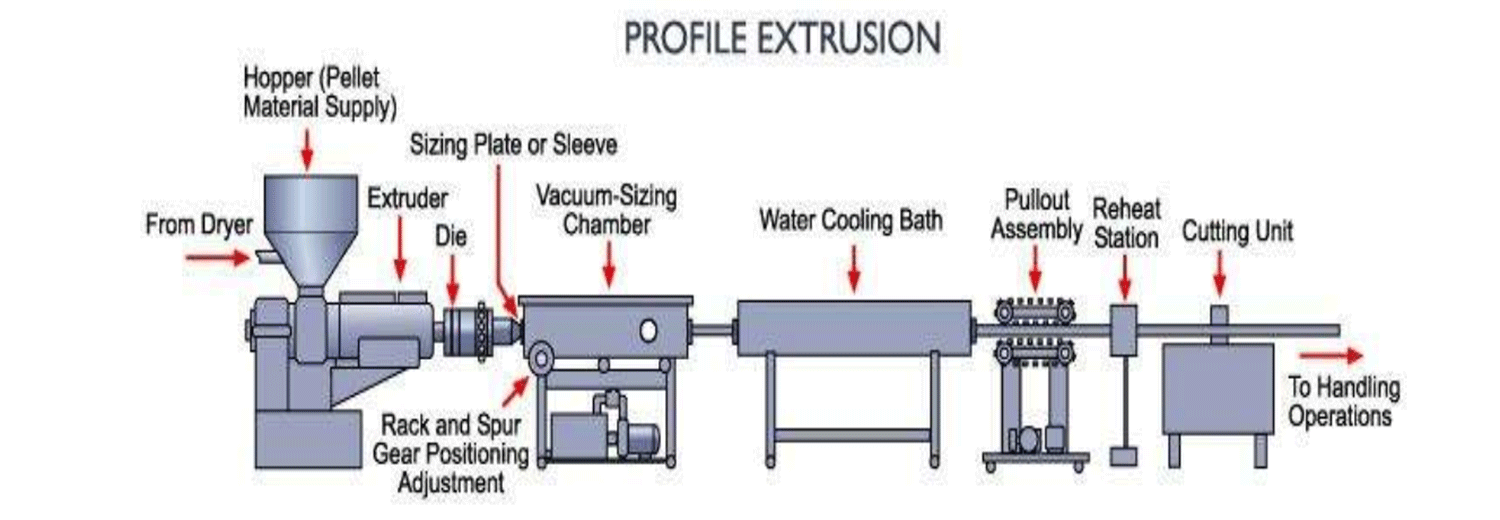
UNIT INTRODUCTION
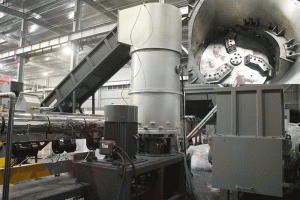
Compacting Force Feeder
Compacting hopper opening by hydraulic system. With glass window and light to check inside working. Barrel base with the water cooling system controlled by magnetic valve by temperature The barrel touched material all made by stainless steel.
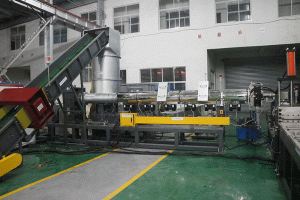
Single Screw Extruder
Single screw Extruder made by sturdy frame, heavy. No vibrating when machine running; The whole frame where installed the gearbox, motor and screw has done the milling working. The frame is build up by the square tube and thick steel on top.

Vacuum Degassing System
With the vacuum degassing system
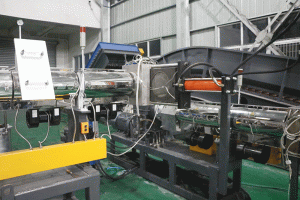
Hydraulic Screen Changer
Double position board model Board made by 38CrMnAl with forging, heating treatment won’t deform after heating using.
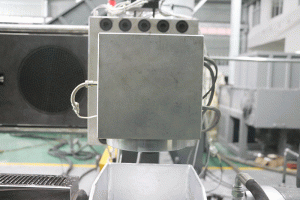
Degassing Die Head
Made by 40Cr material with tempering and quenching treatment. Design as a material disperser so the material comes out as noddle, so it can remove the air and humidity from the material.
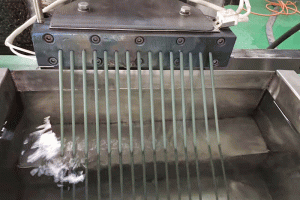
Die Head
Die mold made by the 40Cr material with forging treatment, surface been nitriding treatment and manufacturing by CNC
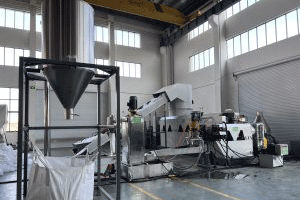
Silo
·The function of the blower is to transport particles to the silo through stainless steel pipes. ·Pipes and silos are wrapped with black sound insulation cotton, which reduces the volume from 82dB to 68dB. ·Pipes and silos are made by SUS 304.
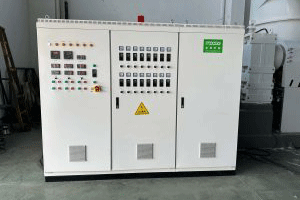
Electrical Control Cabinet
·Inverter: ABB/DELTA. ·Contactor: Schneider. ·Adopt CE safety electrical components. ·Solid state relay is optional for heating control. ·Safety interlock principle applied in the system
TECHNICAL DATA
Specification
Model | GSC2-85/100 | GSC2-100/100 | GSC2-130/130 | GSC2-160/160 | GSC2-180/180 |
Output(KG/H) | 150-200 | 250-350 | 450-550 | 650-750 | 800-1000 |
Installed power | 140 | 205 | 290 | 410 | 580 |
Labor requirements | 2-3 | 2-3 | 2-3 | 3-4 | 4-5 |
Factpry area(L*W*H) | 10*5*4 | 12*5.5*4 | 14*6.5*4 | 16*6.5*4 | 18*6.5*4.5 |
COOPERATION PARTNER
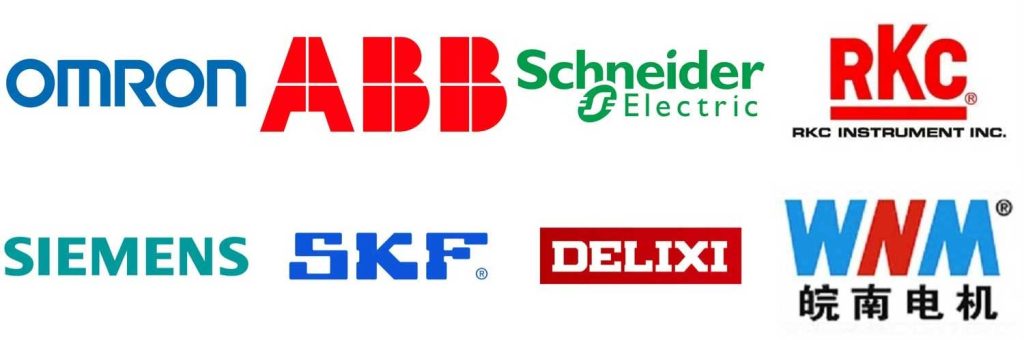